Silver paste, Copper paste, Conductive silver paint and Conductive ink
Conductive Silver Paste's Various Applications
The conductive silver paste produced by Kunshan Yosoar is widely applied in the electronics field or the chemical industry. Generally speaking, silver paste contains special polymers, but only a small amount, so it has adhesive properties and does not reduce the loss. Air performance, more uniform drying.
A viscous slurry of a mechanical mixture of high-purity silver particles, binders, solvents, and additives.
The composition, content, shape and size of silver paste are closely related to the properties of silver paste.
Silver particles are the main component of silver paste. The higher the silver content, the better the conductivity.
The electrical conductivity is related to the size, shape, and silver content of the silver paste.
Divided into high temperature silver paste, medium temperature silver paste and low temperature silver paste.
Silver powder can be used to make paste, with good conductivity, and can be used in many fields.
Used in Membrane switch
Membrane switch, also called light touch keyboard, is an integral sealing structure made up of flat and multi-layer combination. It is an integrated light, mechanical and electrical integration that seals the key switch, panel, mark, symbol display and lining board together. A new type of electronic components.
Conductive silver paste can be used on membrane switches. First of all, membrane switches are composed of multiple layers of thin films. Different material properties can be used to play different roles to complete the functions and effects of membrane switches on electrical products.
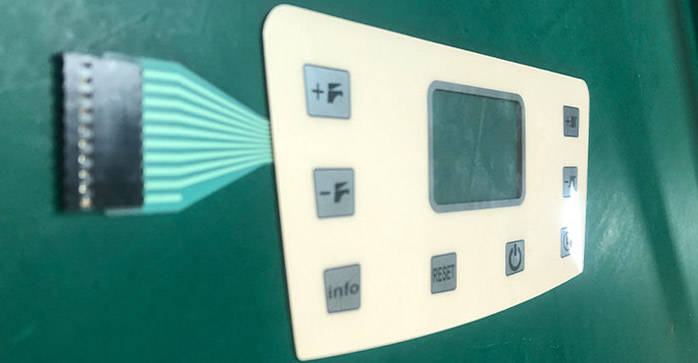
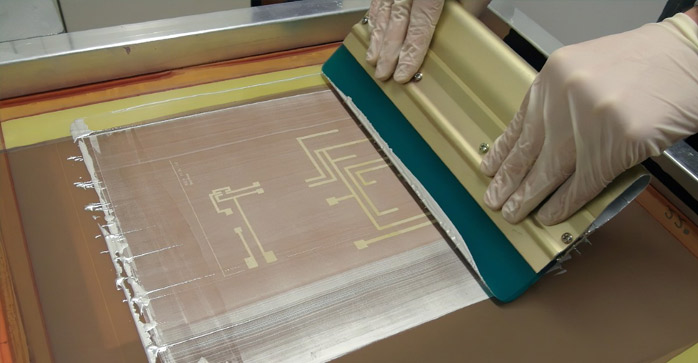
Used in screen printing
The general screen printing means that the screen is used as the base, and then the photosensitive plate can be used to make a screen printing plate with pictures and texts. The five elements are screen printing plate, ink, printing table, squeegee and substrate.
Conductive silver paste can be used in screen printing, mainly refers to the silver paste that is printed on the substrate to allow it to conduct current and eliminate the ability to accumulate static charge. Most of it is printed on non-conductive substrates such as glass, plastic, ceramics, etc. .
Yosoar——Silver Paste Manufacturer Worthy Of Your Trust
Conductive fillers, solvents, adhesives and additives together form the silver paste produced by Kunshan Yosoar. This conductive silver paste’ filler is silver powder which has very good conductivity. There are also pastes made of other copper powders, but The effect is not as good as that of silver powder.
General conductive silver will have good conductivity, good adhesion, and good oxidation resistance and acid resistance. Common application areas include shielding circuits, computer keyboard circuits, membrane switches, and the printing of flexible circuits.
Yosoar conductive paste has the excellent quality, stable performance, wide application, and can be customized according to needs. Yosoar has a professional silver paste research and development team with rich experience, which can ensure the sustainable technology development and research application of the conductive silver paste. As long as you send us your detailed requirements and applications, Yosoar provide will supply you suitable silver paste products and services.
- Manufacturing
- Certification
After screen printing, leveling, drying, sintering and other processes, silver paste can form a conductive network on the ceramic substrate to make thick, thin film integrated circuits and resistors, carbon film potentiometers, round chip tantalum capacitors, Electronic components such as membrane switches, flexible circuits, and ceramic capacitors. Solar cell electrodes, light-emitting diodes (LED), organic light-emitting diodes (OLED), printing and inkjet printing high-resolution electrical conductors, conductive adhesives, sensitive components, etc. can be seen everywhere.
I know that you are looking for a suitable silver paste. Maybe you want to know more information about the conductive silver paste. Therefore, this guide will answer all the questions you have been asking about silver paste. Do you want to understand the composition, performance, quality and application of conductive silver? This guide contains all the information you need. Please continue reading, and Yosoar will give you a satisfactory answer.
The material industry has an increasing demand for conductive silver paste with silver and other metal powders as the conductive functional phase, and the technical requirements are getting higher and higher. In simple terms, silver paste refers to the silver paste that is printed on the substrate to enable it to conduct current and eliminate the ability to accumulate static charge. It is generally printed on non-conductive substrates such as plastic, glass, ceramics, and cardboard. Conductive paste is composed of conductive phase silver powder, binder, solvent and trace additives to improve performance. It can be divided into polymer conductive paste and sintered conductive paste.
¤ Compared with paint, what are the differences between conductive silver paste?
—Flexibility
—Conductivity
—Different resins require special resins
—Special additives
—Good printability
—Rheological properties
—Similar to ink
—Fineness
—Viscosity
—Line width
—Film thickness
—Resistivity
—Hardness
—Roughness
—Mechanical properties
—According to performance classification
According to different curing processes, it can be divided into three categories: sintered silver pastes, heat-cured silver pastes, and UV-cured silver pastes. Sintered silver paste uses glass powder or oxide as an inorganic bonding phase and generally needs to be sintered at a temperature above 300°C to decompose and volatilize the organic matter in the paste to form an electrode or conductive wiring film layer. The curing type silver paste uses polymer as the bonding phase, which can usually be cured into a film at low temperatures (generally below 150°C). Compared with the two, each has its advantages. The former has a dense film layer with better conductivity and adhesion to the substrate; the latter has a simple process and high film-forming efficiency. Compared with the former two, the adhesive phase in UV-curable silver paste is more complicated, and at least it should have UV-curable monomer, photosensitizer and a cross-linking agent. Its curing mechanism is also relatively complicated. The photosensitizer is excited to become an activated molecule under the action of ultraviolet light, and the activated molecule induces a copolymerization reaction of the photosensitive polymer, and finally crosslinks to form a network structure. Since film formation does not require heating, UV-curable silver paste is often used for bonding and conducting heat-sensitive elements and components that do not require heating to be cured.
The use of conductive silver paste is very wide, and many kinds of corresponding conductive silver paste are being developed.
—Classified according to a wide range of usage
It for membrane switch based on PET
Low-temperature silver paste for flexible circuit board
Silver paste for single-board ceramic capacitors
Silver paste for varistor and thermistor
Silver paste for piezoelectric ceramics
Silver electrode conductive paste for carbon film potentiometer
Conductive silver paste refers to the silver paste that is printed on conductive substrates so that it has the ability to conduct current and eliminate accumulated static charges. Generally, it is printed on non-conductive substrates such as plastic, glass, ceramic or cardboard. There are a wide range of printing methods, such as screen printing, letterpress printing, flexographic printing, gravure printing and lithographic printing. Different printing methods can be selected according to the requirements of the film thickness, and the resistance, solder resistance and friction resistance are also different when the film thickness is different.
Because silver powder is the main conductive filler in the conductive paste, there must be silver migration in the silver paste. Silver migration is a problem that cannot be ignored when using conductive paste, so how to prevent and deal with the silver migration phenomenon in silver paste.
—Prevention and treatment of silver migration in conductive silver paste:
(1) Make the gap outside the silver circuit (wire) as wide as possible, and keep the voltage (potential) low;
(2) A layer of carbon paste or blue transparent insulating ink with a thickness of >30μm can be added on the silver circuit;
(3) In order to prevent the accelerated migration of silver in a humid environment, vent holes should be added when designing the circuit;
(4) Pay attention to the hygienic conditions of the printing environment, avoid dust and pinholes when screen printing the insulating coating. If dust and debris fall into the wire and circuit, under certain conditions, it may cause the electrical performance to decrease;
(5) Insufficient curing or excessive solvent of the screen-printed silver paste circuit insulation coating will reduce the insulation performance of the insulation layer, thereby reducing the anti-migration performance of silver in a humid air medium.
—The drying of the conductive silver paste after screen printing should adopt the following three-stage curing method:
(1) 2/3 time (specified temperature);
(2) Place at room temperature for 1~2 h;
(3) Infrared drying takes 1/3 time (specified temperature).
—Conductive silver paste itself has better performance. The same is the silver paste, and its resistance range is different, and each factory does it differently.
—In the same situation of silver paste, the resistance can be controlled by the thickness of the screen. The thicker the screen, the lower the resistance, and vice versa, the higher the resistance.
—In the same situation of silver paste, the resistance can be controlled by the mesh number of the mesh. The lower the mesh, the lower the resistance value. The higher the mesh number, the higher the resistance value.
—In the case of the same mesh, silver paste, and film thickness, the greater the screen tension, the lower the resistance, and vice versa.
—The more inclined the scraper is, the lower the resistance value is, and vice versa.
The price of conductive silver paste is closely related to the ingredients inside, especially the particle size, morphology and content of the added conductive filler metal silver powder.
Metallic silver powder is the main component of conductive paste, and its conductive properties are mainly realized by silver powder. The content of silver powder in the paste directly affects the electrical conductivity. In a sense, the high content of silver is beneficial to improving its conductivity, but when its content exceeds the critical volume concentration, its conductivity cannot be improved. The content of silver in silver paste is generally 60 to 70%. The size and shape of silver particles are closely related to the conductive properties of silver paste. The conductive particles used to make conductive printing materials are preferably flake, flat, or needle-shaped, and flake particles are especially superior. The round particles are in point contact with each other, while the flake particles can form surface-to-surface contact. After printing, the flake particles overlap each other in scales at a certain thickness, thus showing better electrical conductivity.
Conductive silver paste is a material in which conductive powder is uniformly added to the adhesive and cured to form a conductor. Used for the formation of electronic circuits, the formation of electrodes of electronic components, the extraction of lead terminals, and the formation of circuit contacts.
Normal temperature/heat-curing silver paste: used for the formation of printed circuit board circuits, the formation of capacitor electrode leads, resistance terminal electrodes, crystal newspapers, switch contacts, through holes, resistance adjustment, potentiometer electrodes, static electricity prevention, etc. High-temperature sintered conductive silver paste: used for multilayer ceramic capacitors, mica capacitors, thermistors, non-linear resistors, piezoelectric components, kinescopes, solar cells, chip resistors, network resistors, thick-film hybrid ICs, etc.
Thick film conductive silver paste is generally composed of three main components: functional phase, bonding phase and organic carrier.
The functional phase in the silver paste determines the conductivity of the paste and affects the physical and mechanical properties of the film; in the conductive silver paste, the functional phase is generally metal, alloy or a mixture thereof.
The role of the bonding phase in the silver paste is to make the film layer and the substrate firmly bond, usually, glass, oxide crystals or their mixtures are used as the bonding phase. The choice of the bonding phase has a certain impact on the mechanical and electrical properties of the film. . The organic vehicle is a solution formed by dissolving a polymer in an organic solvent. It is a carrier for the functional phase and the binder phase particles. It can control the rheological properties of the slurry and make it suitable for screen printing.
The volatile phase in the organic vehicle in the conductive paste generally uses alcohols, and the non-volatile phase mostly uses ethylcellulose or its derivatives. The performance of thick film conductive paste varies according to the application, usually including adhesion strength, solderability (wetting); in addition, conductive silver paste is also required to have good manufacturability, such as thixotropy, printing reproducibility And sinterability. The key to determining the above properties is the composition of the silver paste, the ratio between the phases and the preparation method of the paste.
Here is a brief introduction to the general preparation process of silver paste. Generally, silver powder, glass powder, and organic carrier are prepared according to the proportions, and they are mixed and dispersed. In order to make the metal powder, glass powder and the organic carrier form a uniform and fine silver paste, the powder must be mixed with the carrier first, and then ground to make it evenly dispersed in the carrier. The powder and the carrier are generally first packed in a stainless steel or polypropylene container and mixed in a planetary mixer so that the powder is infiltrated by the carrier and at the same time the larger agglomerates are broken. This process continues until the larger agglomerates are crushed and all powders are infiltrated by the carrier. After the powder and carrier are properly mixed, they are transferred to a three-roll mill for grinding. During the rolling process, the huge shearing action causes the agglomerates to be further crushed, and the powder is completely infiltrated, thereby making a silver paste.
It uses silver powder as the conductive filler. The shape and performance of the silver powder are closely related to the overall performance of the silver paste. Generally, the following performance characterizations are performed on the silver powder.
—The particle size is detected by a laser particle size analyzer, which reflects the size and distribution of the aggregated particles of the silver powder; for the same grade silver powder, the smaller the particle size, the better the dispersion.
—The specific surface area represents the surface area per unit mass of silver powder, which is measured by a nitrogen adsorption specific surface area meter; the larger the specific surface area, the smaller the particle size of the silver powder, and the higher the oil absorption in the slurry system.
—The bulk density means the bulk mass of silver powder per unit volume. With the same particle size distribution, the smaller the bulk density, the smaller the microscopic particle size and the larger the specific surface area.
—Burning loss means the weight loss of silver powder after 550℃ for 0.5 h. It is calculated by mass fraction to determine the silver content after removing high-temperature volatile components in the silver powder.
—Moisture means the weight loss of silver powder after 110℃ for 1 h. In terms of mass fraction, generally, too much moisture will cause poor compatibility between silver powder and organic oily carrier.
—Silver purity reflects the silver content of silver powder after removing chemical impurity elements, and should generally not be less than 99.95%.
In market applications, there are very few truly universal silver powder and conductive silver paste products, which require communication between the upstream and downstream of the industry. There is a process of mutual grinding between producers and suppliers. It can be said that the market applications of silver powder and conductive silver paste are expanded in the process of continuous development and cultivation.
Conductive silver paste uses silver as the main functional phase. Among thousands of electronic paste products, about 80% use various types of silver powder as the main functional phase. Among many precious metals, the price of silver is relatively low, which is conducive to cost control. At the same time, the silver layer can form a continuous dense uniform thin layer on the ceramic surface, which has strong adhesion to the ceramic surface. Therefore, the ceramic conductive layer of the same area and thickness Among them, the capacitance of the silver electrode is larger than that of other electrode materials. However, silver will produce electron migration under the action of an electric field, which will reduce the conductivity and affect the service life of the device. This is a major defect in the use of conductive silver paste in electronic products.
Researchers have conducted a large number of research experiments, among which improving the conductivity of silver paste by improving the size and morphology of silver powder particles is one of the most effective methods. In the conductive silver paste, the morphology and content of the silver powder have a significant effect on the density and resistivity of the thick film paste. Reasonable control of the gradation of the micro-particles and nano-particles of the conductive silver powder can produce conductive silver with denser sintering and better conductivity pulp.
As the most common type of silver paste, the silver paste avoids its own defects of silver migration, while reducing the amount of silver powder in the silver conductive silver paste and reducing production costs. On the one hand, silver powder is developing towards flake and nano-scale silver powder. On the other hand, silver powder is mixed with silver powder by doping base metals (Ni, Al, Cu, etc.) or other conductive materials to make mixed powder or composite powder with silver powder to reduce the amount of precious metal silver powder reduces the cost of slurry production.
Conductive silver paste applied to the membrane switch is a very important type of silver paste, which is mainly composed of a conductive phase, an organic carrier and a modified additive. At present, the electronic market is developing towards low cost, and the domestic low-temperature curing conductive silver paste is used annually in more than 120 tons. Making low-cost, high-performance silver paste is a technical problem that we urgently need to solve.
Most of the printing materials used to print membrane switch circuits are conductive paste, which is a common material for processing electronic components by screen printing. At present, there are many types of silver pastes for printing membrane switch circuits, and there are great differences in performance and quality. The performance of silver paste should be evaluated in terms of resistivity, solid content, the particle size of metal particles, bonding strength, curing temperature, etc., and then reasonably selected.
Since silver paste is expensive and its quality is related to the electrical performance of the membrane switch, it should be selected carefully. The viscosity of conductive silver paste is more viscous than ordinary ink, and it also contains metal solid components. Therefore, you should pay attention to re-scraping when printing. The presence of various solvents and additives in the silver paste has a certain effect on the resistivity. To release them from the conductive circuit, it is mainly dependent on hot air drying to volatilize. The drying temperature is generally controlled at 85~90℃, and the temperature is kept constant for 40min under hot air. The practice has proved that the resistance of incompletely dried conductive patterns is often more than tens of times higher than that of thoroughly dried patterns. Therefore, the drying quality is also a major aspect of the quality of the membrane switch.