Different Sizes and Morphologies Copper Powder Manufacturer
Kunshan Yosoar has a complete series of processes for the production and sales of this, and conforms to the ISO9001 quality management system standard. The produced copper powder is used in the production of microelectronic devices and used to manufacture the terminals of multilayer ceramic capacitors. It can also be used as a catalyst in the synthesis of methanol from carbon dioxide and hydrogen. It can also be used as petroleum lubricant and medicine, electroplating, coating industry, etc.
We can provide copper powder to meet your application field and solve various problems in use.
It has better formability, better conductivity, and low oxygen content,there are different particle size options
It is a metal powder with red luster, generally insoluble in water,keep away from fire and heat sources.
Because it is in contact with air more, it is easy to be oxidized, so please pay attention to storage
It is relatively fine, easy to oxidize and agglomerate, the particle size is greater than or equal to 1um
The color is relatively uniform, shiny, and low resistance. It is made into conductive and shielding materials.
It can be used in different fields to ensure the best conductivity and porosity of the application product.
Used in catalyst
Copper powder can be used as a catalyst to synthesize organic materials with dimethyl, usually ammonia methane (CHaCl) and silicon as raw materials. Now the process of electrolytic copper powder is gradually improved. The previous electrolytic copper powder has limited application due to its relatively large particle size. Now it is constantly improving and broadening its application in the field of catalysts.
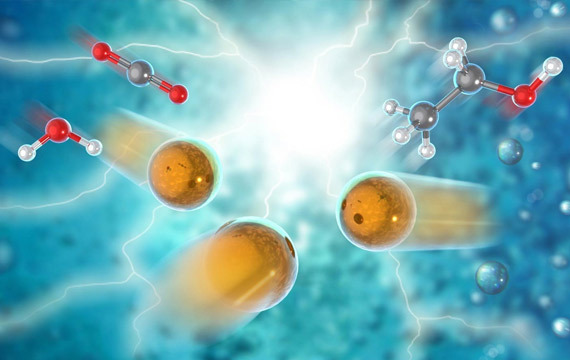
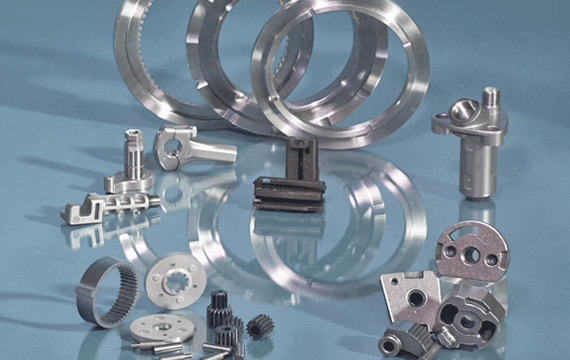
Used in powder metallurgy
Because copper powder has good corrosion resistance and mechanical properties, as well as electrical and thermal conductivity, and can be easily processed into complex shapes, it is often used to manufacture forgings and powder metallurgy products.
Copper powder can be mixed with other materials to form metallurgy with multiple functions. For example, copper and nickel can form an alloy to resist the corrosion of sea water. The alloy made of zinc and copper, called brass powder, can be used in valves, water pipes, etc.
Used in conductive materials
Copper powder can be used on conductive materials, because copper powder can be made into complex electrical and electronic components by metal injection molding, and it has good thermal and electrical conductivity.
We can use high-purity copper powder to increase the final density of parts and thus improve electrical conductivity and thermal conductivity. Therefore, copper powder is widely used in conductive materials.
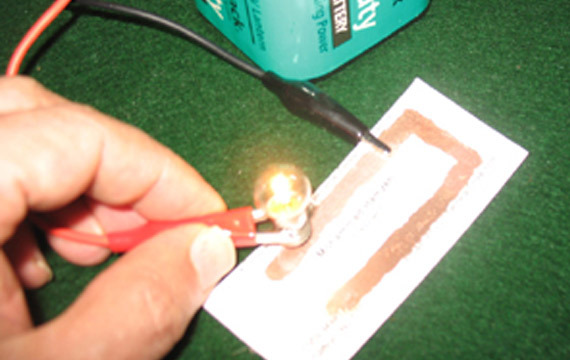
Yosoar: Your Reliable Copper Powder Supplier in China
Kunshan Yosoar is famous for the research and production of various copper powders. The metallurgical field is the largest industry that needs electrolytic copper powder,
The particle size of micron is about 1um-45um, such as there are 200 mesh, 325 mesh, 800 mesh and so on, including spherical, flake and dendritic shapes can be selected, We have different sieves to make the size you need.
Yosoar has its own professional technical team and maintains long-term cooperation with many universities across the country.
The company strictly follows the regular ISO9001 quality management system standard and has complete analysis and testing equipment and testing production lines to ensure that it provides customers with high-quality products and mature application processes.
Kunshan Yosoar has advanced production technology and can provide copper powders in many sizes from nanometers to micrometers, as well as spherical, flake, dendritic, and other shapes.
- Manufacturing
- Certification
Pulp point solution can solve the problem of metal enrichment and recovery and is a promising hydrometallurgical method. Ultrasound is very beneficial in the field of hydrometallurgy and has many applications as well including material modification, and material preparation.
The manufacture and use of copper powder.
Copper in the last century 80 mid-decade developed a new fine chemical material, has been made a better effect on the catalyst oil, lubricating oil additives, conductivity, and electromagnetic shielding materials, human anti-aging drugs and other products. It is mainly produced in two categories: mechanical physical method and liquid phase chemical reduction method.
There are various methods of the preparation of copper powder including the electrolyte by cathode reduction method; preparation of ultra-fine product by a new type of cathode rotating device; preparation of ultra-fine product by ultrasonic electrolysis method; production of copper alloy powder by atomization method; self-suspension directional flow Nano-copper powder is prepared by the method; the nano-powder is prepared by the hydrothermal synthesis method; the ultrasonic field-assisted slurry electrolysis method is to directly prepare the fine Cu powder by using a copper concentrate.
It has recently been discovered that the product is used in conductive filler preparation of conductive ink when copper is added an amount of about as much appropriate, when we add copper powder, the amount of its conductive ink of conductivity can have any specific impact. Recently, it has been observed that a new field of printed electronics has emerged in the manufacturing technology of electronics. Well, the key material behind this increases manufacturing technology is the use of conductive ink, and because of this advancement in this field, the conductive ink of it has also gained much popularity. Copper conductive ink, the main component comprising a binder and a conductive filler copper, wherein, the binder is a conductive ink primarily the deposition material, and with copper, and the conductive ink is generally determined by the filler that it has. The binder is the phenolic resin whereas the conductive filler is the copper powder of micro-level. By a screen printing technique preparation, a conductive copper film on a copper Lee phenol resin conductive ink coating are at different positions tested resistivity, taking five data points, seek Its average value. The conductive coatings of the resistivity with a conductive filler copper mass fraction of the variation shown in FIG. The appropriate amount of this included in it is 60 %~ 80 %. This level being less than 60 % is referred as copper deficiency, the conductive ink is too thin, resulting coating of copper that is conductive cannot be sufficiently in contact with, the conductive coating of the resistivity is too large. While when copper is added an amount greater than 80 % conductive ink becomes viscous, brushing performance is generally not satisfactory, further it is difficult by screen printing and even does not form a conductive coating, the conductive coating resistivity greatly even not conducting. The figure can be seen that with the copper powder added amount increases, the conductive coating of the resistivity presented to decrease the rise in the trend. Whenever this powder of copper is added in an amount of 70 %, the copper conductive ink coating having the resistivity of the lowest reaches the 53 is. 865 × 10 -3Ω · cm & lt . In the conductive ink specific application to be selected appropriate to the product and whenever the amount that is added is too little or too much are generally not conducive to the conductive coating of resistivity.
More on copper powder application aspects of the relevant issues, with Yosoar contact.
The surface treatment is used to improve the copper oxidation resistance and improve the conductive paste performance of the method. One kind of processing method is the copper surface is deposited or coated with a layer. These layers may include those of gold, silver or nickel, and other chemical properties more stable the metal, whereas if we generally consider then, silver is indeed one of the most common coating material. If we talk about another method of treatment, then it is to use an organic acid process copper generating acid copper salts may be of copper play a protective role. Selecting lactic acid and D the EAP D (two 3- ethyl- amino -1,2 -propanediol ), respectively, and common to the copper surface for treatment.
Further, if we see the surface treatment of the copper conductive paste properties of impact, we will go through different surface treatment of copper and ERL4221- acid anhydride matrix mixed, prepared as a filler in an amount of 75 % of the conductive paste, in a nitrogen atmosphere in 200 is deg.] C cure 1h, the results of the volume resistivity are shown. Acid copper is adsorbed on copper surfaces plays a protective role, at the same time by thermal decomposition to produce nano copper also facilitate conductivity of the lift. DEAPD can generally result in creating a coordination with the overall surface of the copper powder, whereas if we take into consideration the structure, then because of being dendritic, it results in an effective blockage of oxygen and this ultimately prevents the oxidation of the powder of copper.
When the acid copper and DEAPD simultaneously exist, the can of copper plays a dual protective effect. Anti-aging properties are also conductive paste is an important performance one, directly affect the conductive paste performance in the use of reliability. We for through the different treatments of this preparation of the conductive paste conducted a preliminary aging test, to explore the conductive paste at high-temperature underperformance stability.
Test conditions of air atmosphere, 85 at ℃ aged 16 8H, each after 24h sensing a conductive paste material resistivity. It can also be generally observed, without any processing of the copper powder made of the conductive paste material resistivity as the aging time increases quickly rise, treatment to obtain the conductive paste material resistivity able to maintain better the stability.
Using lactic acid and D the EAP D while on the copper surface for treatment, the general paste prepared, the conductive paste properties, use, and stored procedures are of electrically conductive filler copper play a protective role, effective to enhance the electrically conductive filler of the oxidation resistance and copper conductive paste of the electrical properties and aging properties.
More about the conductive paste performance and application aspects of the relevant issues, with Yosoar contact.
Copper low prices, applied widely, recently there are a lot of customers to consult spherical, then how to select copper? Select how the morphology of copper powder relatively appropriate? The key is to look required the performance and applications. Common copper roughly is divided into a spherical shape and type spherical, dendritic copper, flaky , nano-copper, and other special morphology of the overall powder of copper and the like. Most of the preparation of spherical, a general method for obtaining a copper powder is generally of a spherical
/class spherical ( we define Powder periphery as the center of the distance difference in a certain range in the powder is spherical / class spherical powder ), spherical / class spherical having a low porosity and a relative sliding friction coefficient, good extensibility and ductility, and other materials mixed while having good miscibility. Dendritic means having a dendrite -like morphology of the copper powder, which has a more complex geometry of the structure and the relatively larger the surface roughness, thus having greater the specific surface area, the particles with each other in contact with the contact point of the number of significant increases, therefore, the use of most small amounts of filler material to the maximum increase slurry of conductivity. Shape presents a sheet of copper, it referred to a sheet of copper. The product generally acts as a conductive coating material, the surface in contact with the sheet-like product of charge of conducting more advantageously, smooth surface can increase the contact area, thereby improving conductivity. Copper nanowire refers to an aspect ratio in 1000 above the nano copper, copper nanowires having a large aspect ratio, exhibit high catalytic activity, in the petrochemical, fuel cells and other art has a broad application prospect. E.g. copper nanowires made the film as a touch screen, can be reduced intelligent products of cost . In the application process, typically the different morphologies of copper mixed with the use, such as spherical, dendritic, and a sheet, to use each of the advantages to achieve better the performance results. More about the spherical copper power of choice and application aspects of the relevant issues,with Yosoar contact.
Using high-energy mechanical ball mill pretreatment and ultrasonic field-assisted slurry electrolysis, the copper concentrate can be directly used for the preparation of a copper powder that is fine with a particle size of fewer than 10 μm. Ultrasound can significantly improve the dispersion performance of copper powder; with the increase of current density, the particle size of product decreases, and if we consider the overall specific surface area, then it increases, indicating that increasing current density generally benefits the overall formation of fine. The leaching rate of copper gradually increases with an apparent increase in the temperature, and the particle size of it also similarly increases when compared to the increase of temperature. Therefore, to obtain the highest possible leaching rate and the finest product, an appropriate point solution temperature should be selected. After the fine is surface treated with oleic acid and acetone, the purity of copper is improved, and the oxidation resistance is improved.
The increase of the sintering temperature will cause an increase in volume shrinkage, decrease in porosity, and decrease in permeability for three types of copper powder sintered bodies with different characteristics. The difference in the essential characteristics of the powder makes the larger specific surface area have larger surface energy and higher sintering temperature sensitivity. Among them, the shrinkage of the dendritic sintered body increases by 40%, and the porosity decreases by about 50%. In addition to the impact of porosity reduction, the permeability of the sintered body caused by the actual characteristics of the powder has a key impact on the permeability. Although the porosity of the dendritic sintered body is high, But the permeability is relatively small, and the spherical sintered body has the largest permeability.
Thermal grease, also known as thermal grease, is a non-drying grease and thermal conductive material by adding thermally conductive filler to the liquid polymer matrix material, which is applied between the heating element and the heat dissipation device during use so that it is in full contact. In order to gain this reducing contact thermal resistance, copper powder, especially ultrafine, has the characteristics of small size effect, surface effect and extremely high thermal conductivity, so it is often used as a filler for thermally conductive paste.
Due to the high surface activation energy of ultrafine, it is easy to oxidize in the air and has poor dispersibility, which greatly limits the further application of ultrafine. The general reducing agent that is used in this regard is hydrazine hydrate, choosing different surfactants, using the glucose pre-reduction method, and controlling the reaction conditions to prepare ultra-fine copper powder. The product with higher purity and better appearance is prepared, the raw material cost is lower, and the oxidation product is nitrogen, which does not cause environmental pollution.
If we generally make a comparison between the overall effects of various drying methods on the bulk density and specific surface area of ultra-fine, the results are quite amazing and it is usually observed that the ultra-fine after freeze-drying has a smaller particle size, and its bulk density and specific surface area are the largest. The influence of copper powder particle size found that the usual particle size of the ultrafine after freeze-drying was the smallest, which was 0.58μm.
By comparing the effects of different drying methods on the overall surface appearance of the ultrafine, it is found that the freeze-dried ultrafine copper powder has the best surface morphology. It is a spherical powder with better dispersibility. The overall particle size is a bit higher than that of the specific copper powder having an ultrafine shape by comparing different drying methods. The influence of the bulk density and specific surface area of the copper powder that is fine found that the ultrafine after freeze-drying has a smaller particle size, and its bulk density and specific surface area are the largest.
By comparing the effects of different drying methods on the overall various particle size of the ultrafine, it is found that the average particle size of the ultrafine copper powder after freeze-drying is the smallest, which is 0.58μm. By comparing the effects of different drying methods on the surface morphology of the ultrafine, it is found that the freeze-dried ultrafine copper powder has the best surface morphology, which is a spherical-like powder with better dispersibility, with smaller particle size and better dispersion.
By comparing the effects of different drying methods on the overall electrical conductivity of the ultrafine, it is found that the ultrafine copper powder has the best electrical conductivity under freeze-drying. However, other drying methods can usually be in contact with the air, and the oxidation will be small and the dispersion will be better.
It has one of the general advantages of having low resistivity along with low electromigration speed and low price as well. In contrast, if we consider the overall chemical properties of this, them they are relatively active. In the air, powdered copper with a large specific surface area is easily oxidized, and Cu20 and Cu0 are formed on the surface. The film makes its conductivity drop rapidly and even becomes non-conductive. Using base metal copper as the internal electrode of MLCC must have the following characteristics: high powder purity, good dispersion, high sphericity, and uniform particle size. At present, there are many methods for preparing copper powder. If we talk about the most commonly used methods, then they are electrolysis, liquid-phase reduction, mechanochemical methods, etc. However, the powders prepared by these methods generally have weak oxidation resistance, wide particle size, and poor sphericity. This method can prepare copper powder that meets the requirements of MLCC internal electrodes has become a general concern.
The hydrothermal method is a promising material preparation method due to its many advantages. However, there are still many problems in the process of preparing by hydrothermal method. Due to limited conditions, it is impossible to observe the mass migration of substances in the hydrothermal solution. Therefore, the mechanism for improving the uniformity of copper powder particle size is still at the preliminary stage of exploration, and a unified theoretical system cannot be formed; During the process, a small amount of hydrogen will be generated, causing the pressure in the reactor to rise sharply, which has an unpredictable effect on the size and crystallinity of the crystal grains; also, the current preparation of copper powder stays in the micro stage. If the preparation amount is increased, Using the same process parameters may result in poor performance of the prepared powder due to objective factors. At present, these problems still need to be studied and resolved by further experiments.